Maschinensägeblätter
Wir liefern Ihnen das Maschinensägeblatt, das bei Ihnen zum optimalen Sägeergebnis führt!
Unsere Empfehlung für langen Sägespaß
Für den Einsatz von GUHEMA-Maschinensägeblättern empfehlen wir die wenigen, aber wichtigen Spielregeln zwischen Werkstück und Sägeblatt zu beachten, um optimale Schnittergebnisse zu erhalten:
- Sägen Sie nie über Eck an.
- Sägen Sie stets mit Kühlung.
- Spannen Sie das Werkstück fest und verdrehsicher ein.
- Ein neues Maschinensägeblatt muss eingefahren werden. Reduzieren Sie in der Anfangszeit den Schnittdruck um ca. 50%.
- Entfernen Sie mögliche mineralische Rückstände vom Werkstück.
- Kontrollieren Sie von Zeit zu Zeit die Sägeblattspannung.
- Wechseln Sie frühzeitig Ihr Metallsägeblatt! Bestes Indiz: deutlicher Anstieg der Schnittzeit.
- Warten Sie Ihre Metallsäge nach den Vorgaben des Herstellers.
- Passen Sie den Schnittdruck, die Schnittgeschwindigkeit und die Zähnezahl dem Werkstück an. Das folgende Diagramm sowie die Tabelle dienen als Orientierung.
- Beim Einsatz von Positivzahn und Future mit ca. 50% des herkömmlichen Druckes beginnen. Wenn das Sägeblatt in voller Breite im Material arbeitet, muss der Druck kontinuierlich erhöht werden, ohne dass beim Sägen ein Brummton zu hören ist.
Faustregel: Schnittgeschwindigkeit / 2 x Hubweg (m) = Hubzahl/min
Schnittdatenempfehlung
Schnittdatenempfehlung bei Vollmaterial im normal geglühten Zustand für GUHEMA-Maschinensägeblätter basierend auf einer Hublänge von 200 mm.
Für Rohre und Profile Schnittdruck entsprechend der Wandstärke reduzieren.
Material | ZpZ bei Materialabmessungen | Schnittgeschwindigkeit | Blatt / | |||||||
---|---|---|---|---|---|---|---|---|---|---|
Bezeichnung | bis | über | Schnittdruck | je nach Materialstärke | Qualität | Zahnform | ||||
30 mm | 50 mm | 100 mm | 200 mm | 200 mm | Hübe / min | m / min | ||||
unleg. Stähle/Baustähle | ||||||||||
Einsatzstähle, z.B. | ||||||||||
St37-C10-C15 | 10-8 | 8-6 | 6-4 | 4-3 | 2-1,5 | niedrig | 60-100 | 24-40 | Super HSS | normal |
St50-St60 | 10-8 | 8-6 | 6-4 | 4-3 | 2-1,5 | bis mittel | 60-100 | 24-40 | Super HSS | normal |
Vergütungsstähle, z.B. | ||||||||||
C35-C45-C60 | 14-10 | 8-6 | 6-4 | 4-3 | 2 | mittel | 55-80 | 22-32 | Super HSS | normal |
CK45-40MN4 | 14-10 | 8-6 | 6-4 | 4-3 | 2 | mittel | 55-80 | 22-32 | Super HSS | normal |
34CrNiMo6-42CrMo4 | 14-10 | 8-6 | 6-4 | 4-3 | 2 | mittel | 45-50 | 18-20 | Super HSS | normal |
leg. Werkzeugstähle, z.B. | ||||||||||
125Cr1-115CrV3-100CrMo5 | 14-10 | 8-6 | 6-4 | 4-3 | 2 | mittel | 40-60 | 25-40 | Super HSS | normal |
X210Cr12 | 14-10 | 8-6 | 6-4 | 4-3 | 2 | mittel | 25-40 | 10-16 | Super HSS | normal |
Schnellstähle, z.B. | ||||||||||
ABC III-DMo 5 | 10-8 | 8-6 | 6-4 | 4-3 | 2 | mittel | 25-40 | 10-16 | Super HSS | normal |
EMo 5 V 3-B18 | 14-10 | 8-6 | 6-4 | 4-3 | 2 | & höher | 25-35 | 10-14 | Brillant | normal |
nicht rostende Stähle, z.B. | ||||||||||
V2A-V4A | 14-10 | 8-6 | 6-4 | 4-3 | 2 | Sondervorschrift | 25-37 | 10-15 | Brillant | positiv |
Sonderlegierungen, z.B. | ||||||||||
Hastelloy-Inconel | 10-8 | 8-6 | 6-4 | 4-3 | 2 | Sondervorschrift | 20-25 | 10-16 | Brillant | positiv |
Nimonic-Titan | 10-8 | 8-6 | 6-4 | 4-3 | 2 | Sondervorschrift | 10-13 | 4-5 | Brillant | positiv |
AMPCO 18-20 | 10-8 | 8-6 | 6-4 | 4-3 | 2 | mittel | 45-50 | 18-20 | Brillant | normal |
AMPCO 21-26 | 10-8 | 8-6 | 6-4 | 4-3 | 2 | mittel | 40-45 | 16-18 | Brillant | normal |
Stahlguss | 14-10 | 8-6 | 6-4 | 4-3 | 2 | mittel | 50-70 | 20-28 | Super HSS | normal |
Gusseisen | 14-10 | 8-6 | 6-4 | 4-3 | 2 | mittel | 50-70 | 20-28 | Super HSS | normal |
Spezialbronzen | 10-8 | 8-6 | 6-4 | 4-3 | 2 | mittel-hoch | 50-62 | 20-25 | Brillant | normal |
NE-Metalle | ||||||||||
Alu-Bronze-Messing | 8 | 6 | 4 | 3 | 2 | niedrig | 80-120 | 32-48 | Super HSS | normal |
Anwendungsbereich für unsere GUHEMA Future Metallsägeblätter:
ZpZ | Beschreibung |
---|---|
8/10 | Materialstärken von 8-30 mm |
6/8 | Materialstärken von 20-50 mm |
4/6 | Materialstärken von 50-100 mm |
3/4 | Materialstärken von 70-150 mm |
2/3 | Materialstärken über 150 mm |
Unsere Empfehlung für grobe Verzahnungen
Seitlicher Fasenanschliff
Nutzen Sie Ihren Vorteil durch unseren seitlichen Fasenanschliff. Sie erhalten sauberste Schnittergebnisse. Vorzeitiges Ausbrechen der Zähne wird durch den Fasenanschliff verhindert und wegen der leichten Spanabrollung ergibt sich eine geringere Belastung von Blatt und Maschine → Metallsägeblatt und Maschine leben länger.
Den seitlichen Fasenanschliff fertigen wir bis 6 ZpZ auf Nachfrage gerne für Sie. Sprechen Sie uns an!
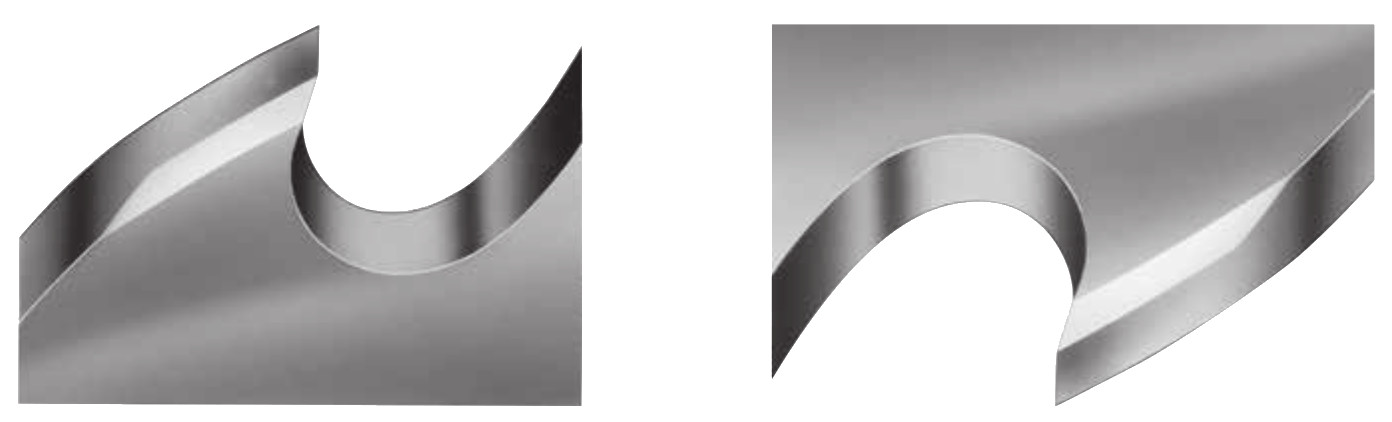
Sie haben Probleme beim Sägen? – Wir haben die Antworten!
Zahnbruch?
Mögliche Ursachen:
- Zu niedrige Zähnezahl gewählt. Mindestens 3 Zähne sollten gleichzeitig im Eingriff sein, auch bei Rohren und Profilen.
- Über Eck angesägt.
- Falsche Einspannung des Werkstücks.
Blattbruch?
Mögliche Ursachen:
- Schnittkanal wurde zusammengedrückt und blockierte das Sägeblatt.
- Falsche Blattspannung.
- Zu grobe Verzahnung für das Werkstück gewählt.
- Zu hoher Schnittdruck.
- Verschlissene Führungslager in der Maschine.
Vorzeitiges Abstumpfen der Zähne?
Mögliche Ursachen:
- Zu feine Verzahnung gewählt.
- Zu hohe Schnittgeschwindigkeit für das Werkstück gewählt.
- Zu hoher Druck (erhöhte Zahnbelastung) oder zu niedriger Druck (Zähne schleifen über das Werkstück, statt einen Span zu heben).
- Unzureichende/falsch ausgerichtete Sägeblattkühlung.
- Falsche Sägeblattqualität gewählt.
- Kein Sägeblattausheben im Rücklauf.
Ungewollter Schnittverlauf?
Mögliche Ursachen:
- Falsche Blattspannung.
- Zu geringe Werkstückeinspannung.
- Zu hoher Schnittdruck.
- Verschlissene Führungslager in der Maschine.
Keine passende Antwort?
Dann sprechen Sie mit einem Experten! Kontaktieren Sie unsere Anwendungsberatung unter +49 (0) 2191 88 67-20.